The Ultimate Guide to Online Laser Cutting Services
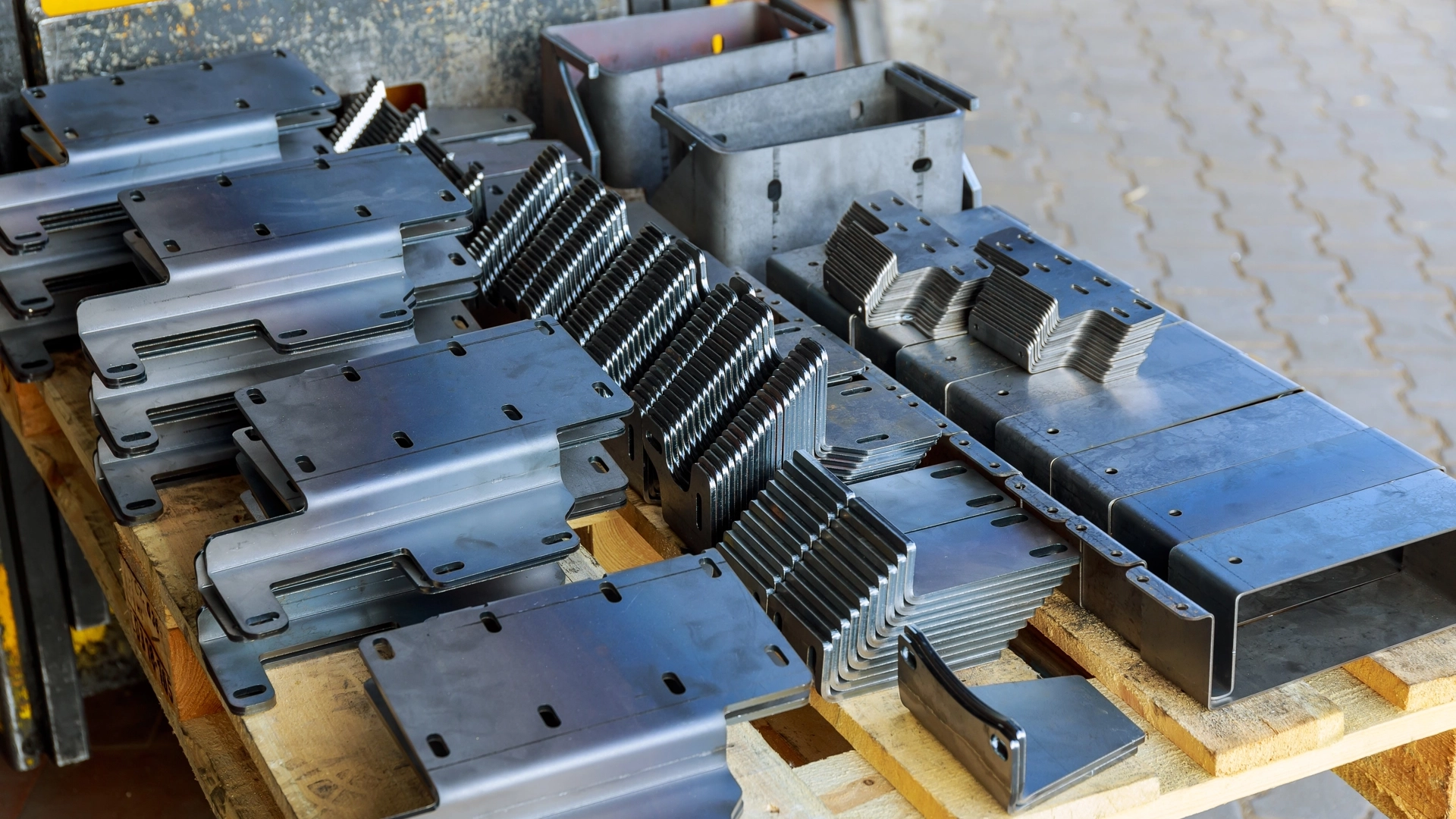
Why Use Laser Cut Sheet Metal for Your Next Project
Sheet metal is the MVP of materials for any project, whether you're a DIY enthusiast or a professional engineer. It’s got versatility, durability, and can be shaped into complex designs with ease. Think about it—whether you’re building a custom car part or a sleek new gadget, sheet metal gets the job done right.
Got a custom project in mind? Sheet metal lets you bring your ideas to life quickly and precisely. You can bend it, cut it, and mold it into almost any shape you need. And thanks to laser cutting technology, you get high precision with tolerances as tight as +/- 0.002 inches. That means your designs come out exactly as you envisioned.
Here are some key perks of using sheet metal:
- Versatility: Can be transformed into complex shapes, making it ideal for a wide range of applications.
- Durability: Provides long-lasting strength and integrity.
- Efficiency: Quick production times help you meet tight deadlines without compromising quality.
Various industries rely on sheet metal fabrication, from Automotive and Aerospace to Consumer Goods and Robotics. Even for DIY projects, it's a go-to material. Its ability to perform in different fields makes it invaluable.
When you choose sheet metal, you’re choosing a material that’s not only reliable but also adaptable to your project's demands. Whether you're working on prototypes or full-scale production, sheet metal's efficiency and precision are unmatched.
Choosing the Right Sheet Metal
Selecting the right sheet metal for your project is crucial. Different materials offer various benefits, so knowing what each type brings to the table helps you make an informed decision.
Aluminum: Light, strong, and resistant to corrosion. It's perfect for projects needing durability without extra weight. Ideal for automotive parts, aerospace components, and even DIY stuff. For more detailed information on the types of aluminum and their applications, check out our material guide.
Steel: Known for its strength and versatility. Carbon steel is great for construction and heavy-duty tasks, while stainless steel adds corrosion resistance, making it perfect for projects exposed to the elements, like outdoor sculptures or custom garden tools. To understand the differences between steel and aluminum, and which might be better for your specific needs, read our comparison of steel and aluminum.
Copper: Excellent for electrical projects due to its high conductivity. It's also malleable, making it suitable for decorative elements and intricate designs, such as custom jewelry or artistic installations.
When choosing sheet metal, consider:
- Thickness: Thicker materials offer more strength but can be harder to shape. Thinner sheets are easier to bend and cut, making them suitable for intricate designs.
- Strength: Match the material's strength to your project needs. Heavy-duty projects require robust materials, while lightweight tasks can use less strong options.
- Flexibility: Some metals are more flexible than others. If your project involves complex bends, opt for materials known for their malleability.
Budget is another factor. While high-performance materials like stainless steel and copper can be pricier, they offer advantages that might justify the cost for specific applications. Aluminum and basic steel are often more affordable, providing a balance between performance and cost. Align your material choice with your project’s performance needs and budget for the best results.
For a more detailed look into material selection check out our Guide on Material Selection
Techniques for Sheet Metal
Cutting sheet metal involves different techniques, both manual and machine-based. Knowing which method to use depends on the thickness and complexity of the metal. Let’s dive into the options.
Manual methods are great for smaller, simpler cuts:
- Hand Shears: Ideal for cutting straight lines or gentle curves in thin sheet metal. They’re portable and easy to use.
- Tin Snips: Perfect for more detailed cuts, especially on thinner sheets. They come in straight-cut, left-cut, and right-cut variations to help you maneuver around corners.
- Jigsaw: Useful for cutting complex shapes in thicker sheet metal. Equip it with the right blade to achieve cleaner cuts.
For more precision and efficiency, machine-based methods are the way to go:
- CNC Plasma Cutter: Great for cutting thicker materials with intricate designs. It offers high precision and speed.
- Laser Cutter: Provides unmatched accuracy, especially for detailed and delicate designs. At Fabworks, our laser cutter achieves tolerances as tight as +/- 0.005". For more detailed information on the capabilities and considerations when designing parts for CNC fiber laser cutting, refer to our Laser Cutting Guidelines.
Choosing the right method involves considering the thickness and complexity of your metal. Here’s a quick guide:
- Thin Sheets (up to 1/16 inch): Use hand shears or tin snips for straightforward tasks. For more detailed jobs, a jigsaw or laser cutter is ideal.
- Medium Thickness (1/16 to 1/4 inch): A jigsaw works well for complex shapes. For precision, opt for a laser cutter.
- Thick Sheets (over 1/4 inch): CNC plasma cutters or laser cutters handle these best, providing clean and precise cuts.
Tips for achieving clean cuts:
- Sharp Tools: Always use sharp blades to avoid jagged edges.
- Proper Safety Gear: Wear gloves, safety glasses, and hearing protection.
- Steady Hands: Maintain a steady hand and slow pace to ensure precision.
Choosing the right cutting technique is crucial for the success of your project. Whether you're crafting or engineering, the right tools make all the difference.
Bending Techniques for Sheet Metal
Bending sheet metal can transform flat sheets into complex, functional parts. Different techniques fit different needs, so let’s break them down.
Hand bending is straightforward. Use simple tools like pliers or a metal brake. It’s ideal for small projects or when you need quick adjustments. But, it’s less precise.
Brake forming is more advanced. A sheet metal brake lets you make consistent bends. Perfect for making multiple parts with the same angles. It’s great for small to medium-sized projects, but it requires some setup time.
Press brakes are the top choice for precision. They can handle large sheets and complex bends. You get high accuracy and repeatability. However, they’re usually found in professional shops, not your average DIY workspace. For those looking for professional-grade results, our comprehensive sheet metal bending service uses CNC bending to achieve high precision and accuracy.
Planning is crucial. Think about where each bend will go to avoid distortion and inaccuracies. This foresight helps maintain the integrity of your design. By understanding these techniques and considerations, you can achieve precise, reliable bends for any project.
Note:
Integrating Hardware Into Sheet Metal Projects
Adding hardware to sheet metal projects can elevate your designs. Using PEM hardware like nuts, studs, and standoffs offers many advantages over traditional methods such as tapping and welding.
Benefits of Using PEM Hardware:
- Enhanced Thread Strength: PEM hardware provides stronger threads, especially in thin materials.
- Reduced Part Count: Combining multiple components into one can streamline your design.
- Ease of Assembly: Quick and reliable installation reduces assembly time and labor costs.
When you integrate PEM hardware, you’re choosing efficiency and strength. Traditional tapping and welding require more steps and can weaken the material. PEM hardware, on the other hand, allows for lighter, thinner materials without compromising durability.
Designing with Hardware in Mind:
- Plan for Placement: Identify where you need hardware and design your parts to accommodate it. Use CAD software to ensure precise placement.
- Check Dimensions: Ensure your holes and slots match the hardware specifications. This prevents misalignment and installation issues.
- Consider Load and Stress: Place critical features outside distortion zones to avoid weakening the material.
For more detailed guidance on designing with PEM hardware, including how to use Onshape for creating designs and integrating PEM components, check out our comprehensive guide on designing with PEM hardware.
Tips for Proper Fit:
- Use a Standard Content Library: Incorporate standard components directly into your design software for accuracy.
- Export as STEP Files: This keeps all dimensions intact and ensures compatibility with Fabworks' laser cutting and bending services.
- Account for Tolerances: Follow guidelines for bend radii and distortion zones to maintain part integrity.
For additional information on hardware installation, including PEM nuts, studs, and standoffs, refer to our hardware guidelines to ensure robust and reliable connections in your sheet metal projects.
Including PEM hardware in your sheet metal project can make a big difference. It improves strength, reduces complexity, and saves time. Proper planning and design ensure you get the best results, making your project both robust and efficient.
Exporting Designs as STEP Files
Exporting your sheet metal designs as STEP files is crucial for precision and ease of transfer. Using popular CAD software like Onshape, you can ensure all relevant design details are preserved. Follow these steps to export your designs correctly:
Using STEP files offers several benefits. First, they maintain all dimensions and design features, ensuring your parts are fabricated precisely as intended. Second, they simplify the transfer process, making it easy to upload your designs to Fabworks' online platform for instant quotes and orders.
For more detailed instructions, you can refer to our guides on exporting step files from various CAD programs.
Properly exported STEP files lead to precise, high-quality parts. Avoid common pitfalls by following the steps above, ensuring your custom projects come to life just as you envisioned.
Tips for Successful Sheet Metal Projects
Planning is crucial. Map out your cuts and bends first. Sketch your design on paper or use CAD software. A detailed plan prevents mistakes and saves time.
Common mistakes to avoid:
- Skipping practice runs: Always make a test part before a full production run.
- Rushing the process: Take your time to ensure accuracy.
Techniques for improving precision:
- Use a laser cutter for detailed designs: Laser cutting achieves tight tolerances, ensuring your designs come out exact.
- Follow bending guidelines: Adhere to our bending guidelines for accurate dimensions.
By following these tips, you'll create precise, high-quality sheet metal parts that meet your project's needs.
Designing and Assembling Sheet Metal Projects
Designing and assembling sheet metal projects is a step-by-step process that demands precision and attention to detail. Let’s break it down.
First, use CAD software to create your design. Programs like Fusion 360 or Onshape help you map out every detail. Ensure your design includes all necessary cuts, bends, and hardware placements. Precise digital designs lead to accurate physical parts.
Once your design is ready, export it as a STEP file. This format preserves all dimensions and details, ensuring compatibility with our laser cutting and bending services.
Steps for Cutting, Bending, and Assembling:
- Cutting: Upload your STEP file to our online platform. Choose your material and thickness. We will handle the rest, providing high precision with tolerances as tight as +/- 0.005 inches across your part.
- Bending: Follow our bending guidelines. Ensure your bends adhere to a .030" bend radius to maintain accuracy. Our machines hold single bends to +/- 0.015" length and +/- 1 degree angle tolerances.
- Assembling: Lay out all cut and bent parts. Use PEM hardware for ease of assembly and enhanced thread strength. For more information about our PEM nut insertion and expert fabrication, check out our Sheet Metal Hardware Service. Plan your assembly sequence to avoid overlaps and obstructions. Secure parts with clamps to prevent movement.
Quality Inspections and Testing
Quality inspections are crucial. Check each component for accuracy in dimensions and bends. Misalignments can cause issues in the final assembly. Use calipers and/or an angle gauge to measure critical features and ensure they match your design specifications.
Tips for Troubleshooting Common Issues
- Misaligned Holes: Check your CAD design and adjust as needed. Ensure holes match the hardware specifications, and are compatible with bend length tolerances.
- Warped Parts: Review your bending process. Ensure you’re following the correct bend radius and distortion zone guidelines.
Final Thoughts
By following these steps and tips, you can create precise, high-quality sheet metal projects. Proper planning, accurate cutting and bending, and thorough inspections ensure your final product meets all required specifications. For additional information on our services, including lead times and tolerances, visit our Frequently Asked Questions page.
When to Seek Professional Sheet Metal Services
Some projects need more than a DIY approach. Professional sheet metal services can make a big difference, especially for complex designs and high-precision requirements.
If your project involves intricate cuts or bends, professional services offer advanced machinery like laser cutters, and CNC press brakes. These tools provide high precision and can handle thicker materials that might be challenging with manual methods.
Here’s when to consider professional help:
- Complex Designs: Need tight tolerances or detailed patterns? Pros have the tech to handle it.
- Large Quantities: Producing multiple parts? Professional services ensure consistency and speed.
- Special Materials: Working with hard-to-cut materials like stainless steel? Experts know the best techniques.
- Critical Deadlines: Tight schedule? Professionals offer rapid turnaround without compromising quality.
Choosing a reliable sheet metal service provider is crucial. Here’s what to look for:
- Quality: Check their precision capabilities. For example, Fabworks offers high-quality sheet metal laser cutting services with cutting tolerances as low as +/- .005".
- Turnaround Time: Ensure they can meet your deadlines. A provider with a high on-time delivery rate is a good sign.
- Customer Support: Friendly, accessible support can make your experience smoother. Look for providers who offer guidance throughout the process.
- Comprehensive Services: From cutting and bending to hardware insertion and finishing, a one-stop-shop simplifies your project. Fabworks also provides a specialized Sheet Metal Tapping Service that enhances the functionality of components through high precision tapping combined with expert laser cutting.
Professional expertise and state-of-the-art machinery can elevate your project, ensuring high precision and timely completion.
Key Takeaways From This Guide
Sheet metal is your go-to material for versatility and durability. It's perfect for custom projects, offering quick, precise, and reliable results. You can shape it into almost anything, from prototypes to finished products.
Cutting techniques vary based on your needs. Hand tools like shears and snips are great for small tasks, while CNC plasma cutters and laser cutters handle more complex jobs. Always use sharp tools and secure your metal to get clean cuts.
Bending methods also differ. Hand bending works for small adjustments, but brake forming and press brakes offer more precision for larger projects. Keep in mind bend radius and spring back to maintain strength and accuracy.
For successful projects, planning is key. Sketch your design, mark your cuts and bends clearly, and practice on scrap metal. Precision tools like laser cutters ensure your designs come out exactly as planned.
Sometimes, professional services are the best route. Complex designs, large quantities, and special materials benefit from advanced machinery and expert handling. Look for providers offering high precision, rapid turnaround, and comprehensive services.
Using sheet metal efficiently means understanding its benefits and applying the right techniques. Whether you're a DIY enthusiast or a professional, the versatility and reliability of sheet metal make it an invaluable resource for any project. Apply these insights to achieve high-quality, precise results in your next endeavor.
Mild Steel vs Stainless Steel
Explore the key differences between yield strength and tensile strength with our concise guide.
Fast Track Your Project .
Seamless process, unparalleled precision, unbeatable speed. Turn your design into reality by beginning your journey with us today.
or drag and drop
.STEP / .STP up to 25MB
Your file are safe, secure and retain all intellectual rights.