Optimizing the cost of Laser Cut Parts
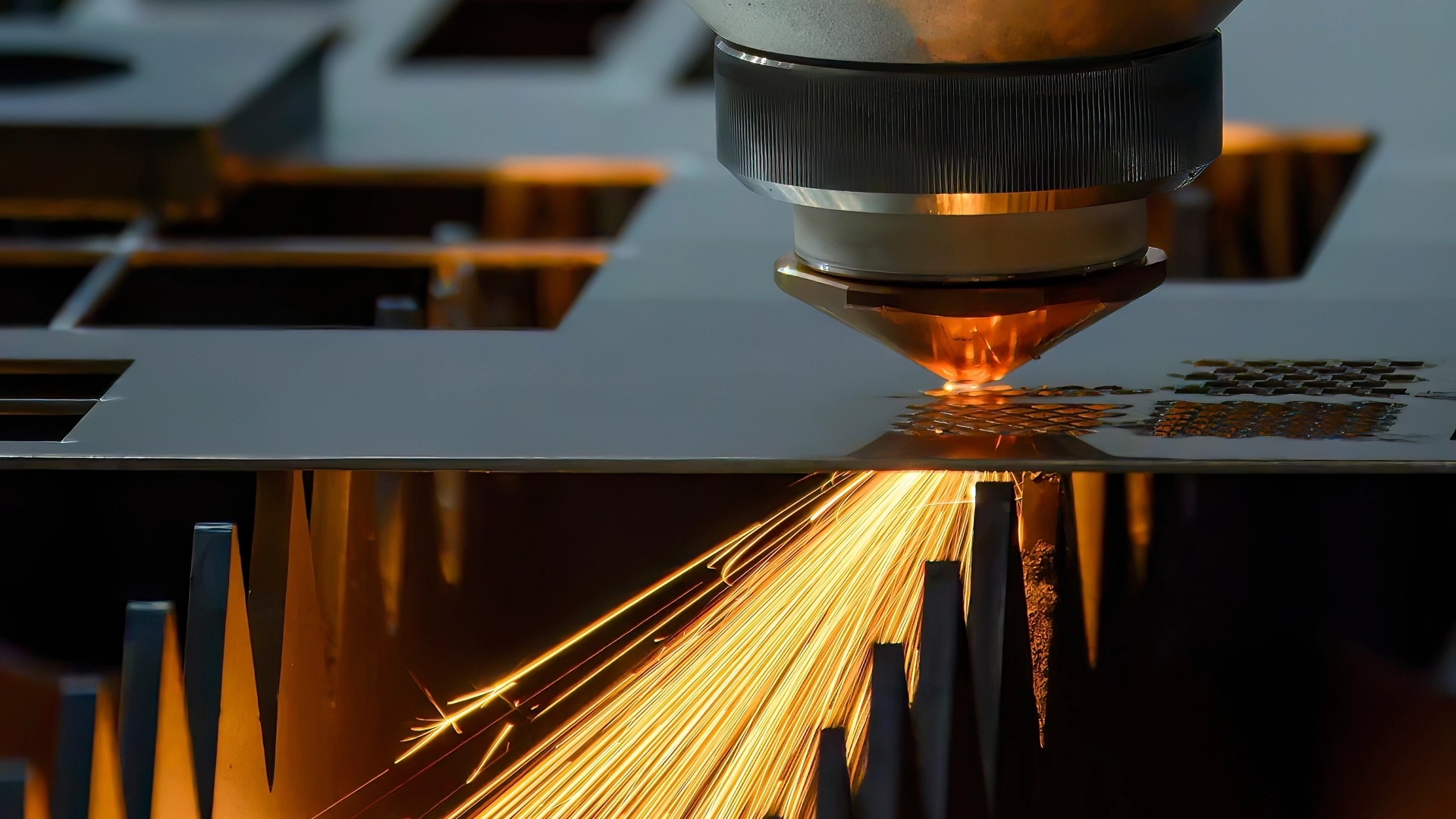
In today's competitive manufacturing landscape, cost optimization is crucial for maintaining profitability and staying ahead of the competition. This blog post will explore key strategies for optimizing parts for cost, focusing on design considerations that can significantly impact your bottom line.
Minimize Overall Material Usage
One of the most straightforward ways to reduce costs is by minimizing the amount of material used in each part. This can be achieved through:
- Lightweight design: Use engineering tricks such as strength bends to create parts that are strong yet use less material.
- Proper sizing: Avoid overdesigning parts with unnecessary bulk, use thinner material when possible.
- Material selection: Choose cost-effective materials that meet performance requirements without excess.
Simplify Part Shapes
Weird shapes often lead to increased manufacturing costs. Make sure your part does not contain excessive unneeded protrusions. As you can see in the images below both parts are similarly priced, even though one contains more material than the other. You can consider "material cost" as the cost of the material that would be used if you cut out the line drawn by a string wrapped tightly around the perimeter of your part.
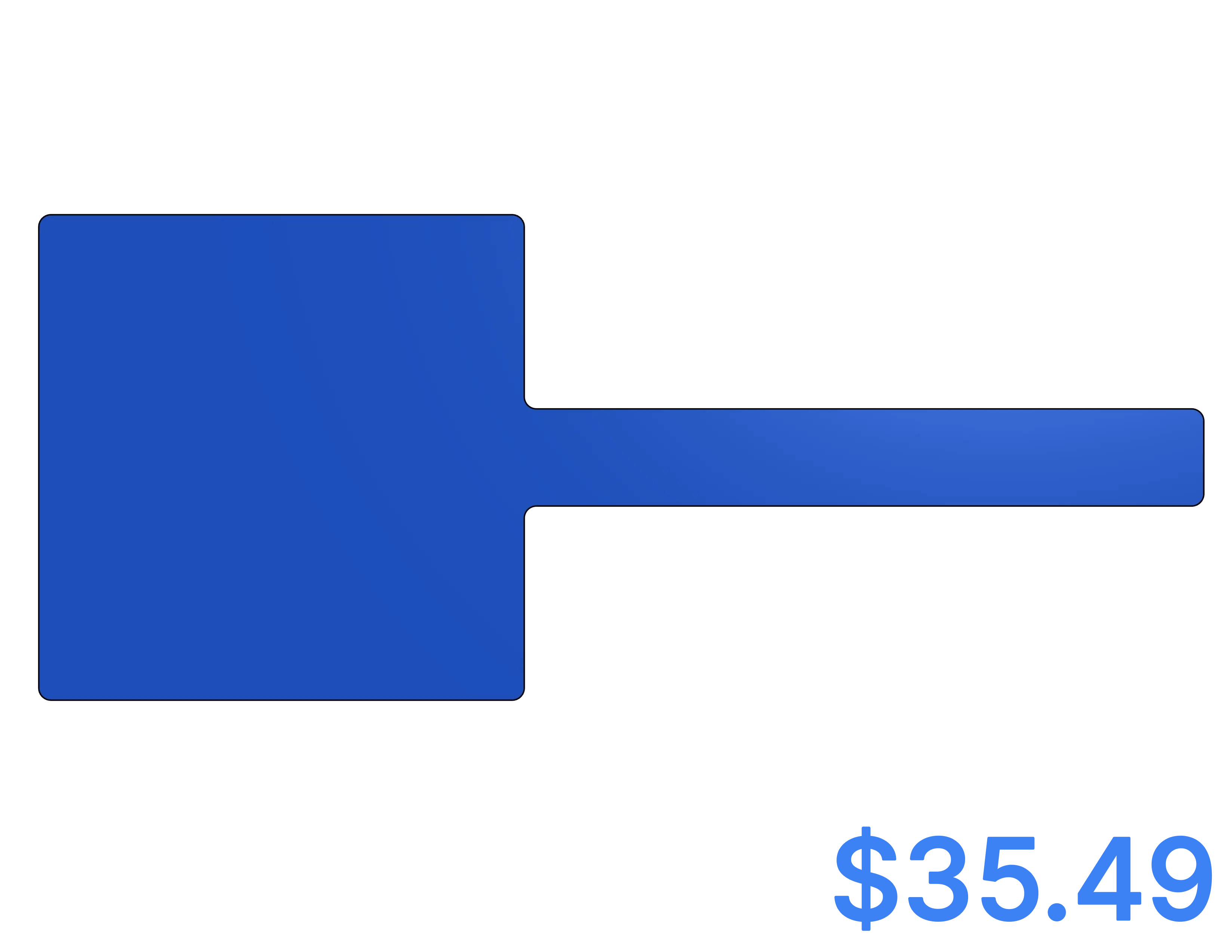
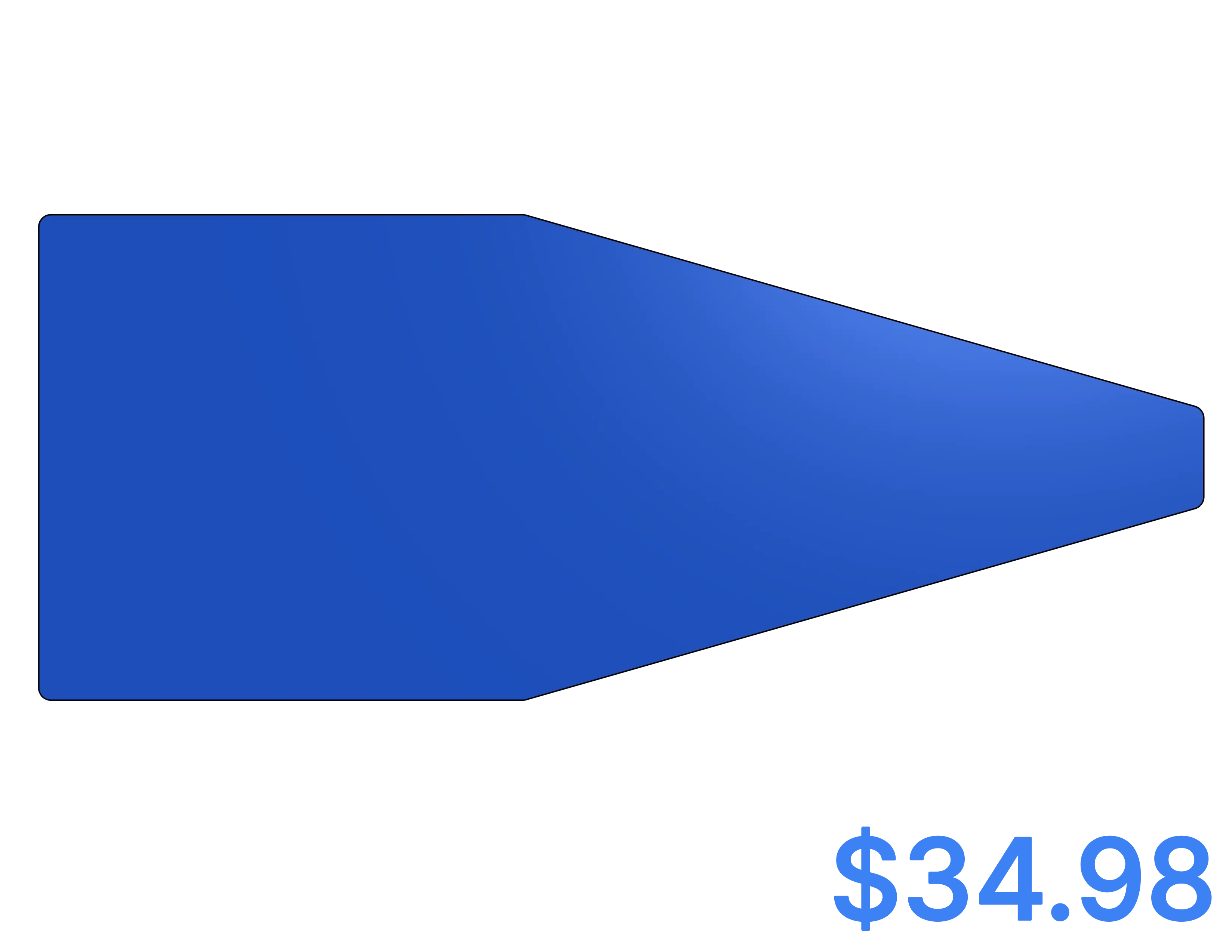
Reduce the Number of Cutouts
While holes and cutouts can be necessary for functionality, they increase manufacturing time and thus cost. To optimize your parts with this in mind:
- Evaluate the necessity of each cutout and hole: Eliminate any that aren't critical for the part's function.
- Combine cutouts where possible: If your part has alot of holes in a line consider making it a single slot or a few if strength permits. This will reduce the number of times the laser has to turn off and on, leading to faster production and reduced cost.
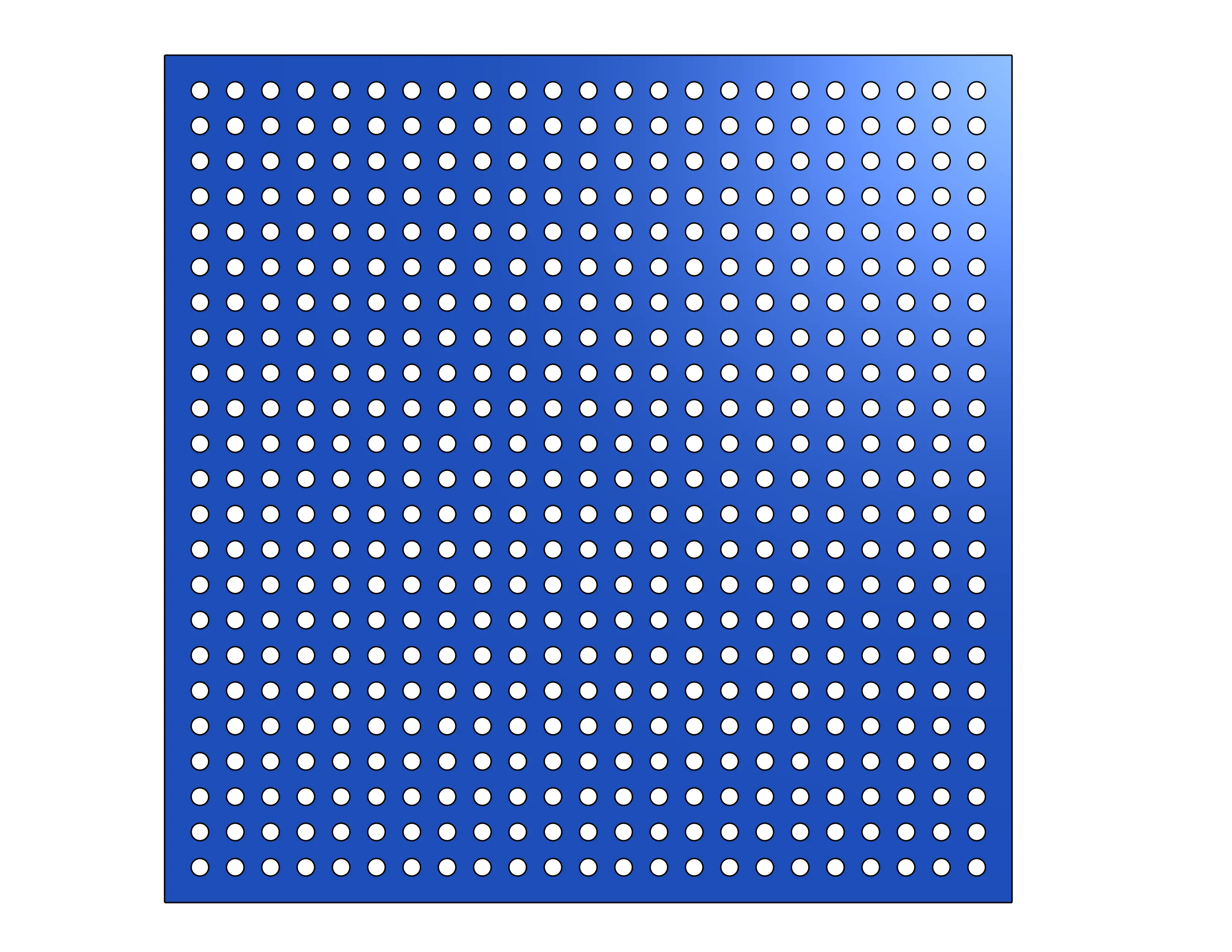
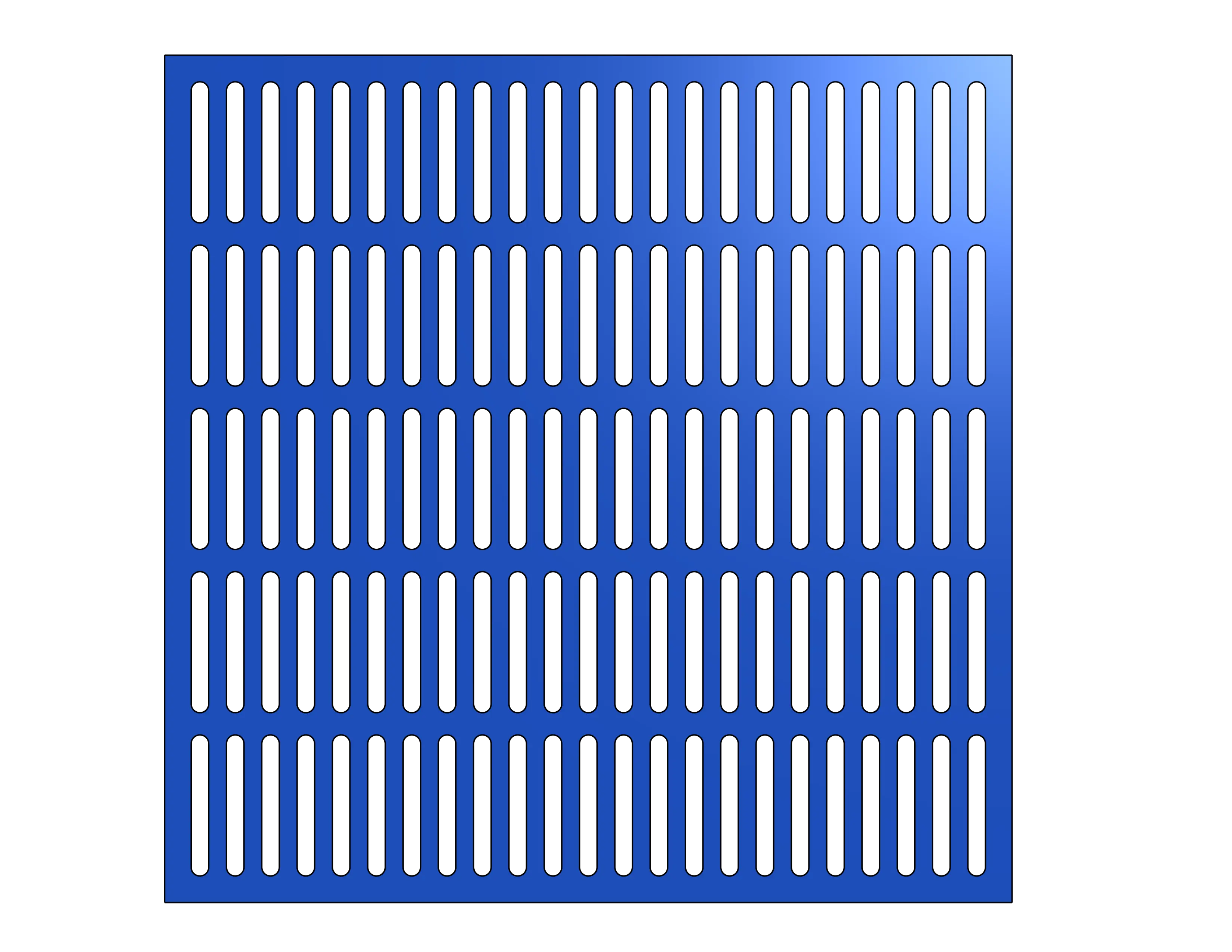
Minimize the Number of Bends
Bending operations add time and complexity to the manufacturing process. To reduce costs:
- Keep the number of bends to a minimum: Each bend requires additional setup and processing time.
- Consider splitting parts into multiple sections: Sometimes, it's more cost-effective to produce several simpler parts and assemble them rather than creating one complex, bent part.
- Use standard bend angles: Its usually easier to bend and validate a 90 degree angle, but something like 92 degrees is more annoying.
Tapping and Countersinking
Tapping and countersinking are common operations in part manufacturing that can significantly impact costs. The most cost-effective approach depends largely on your production volume:
For Small Volume Production:
- DIY Approach: For small batches, it might be more cost-effective to perform tapping and countersinking in-house.
- Benefits:
- Lower upfront costs
- More control over the process
- Flexibility to make changes quickly
- Considerations:
- Requires appropriate tools
- May be time-consuming for complex parts or larger quantities
- Consistency can be challenging to maintain across parts
For Large Scale Production:
If you need hundreds of parts made it might be cheaper to have your parts processed by Fabworks.
- Benefits:
- Reduced per-part costs
- Higher precision and consistency
- Faster turnaround for large quantities
- Considerations:
- May have higher upfront costs
- Less flexibility for last-minute changes
Finding the Break-Even Point:
- Analyze your specific situation: Calculate the costs of in-house vs. outsourced operations for different production volumes.
- Consider factors like:
- Labor costs
- Equipment investment
- Production speed
- Quality requirements
- Determine the volume at which outsourcing becomes more cost-effective than in-house operations.
By carefully considering your tapping and countersinking strategy based on your production volume, you can optimize costs while maintaining quality. For startups or small-scale production, the DIY approach might be more economical. As your production scales up, transitioning to professional fabrication services can lead to significant cost savings and improved efficiency.
Conclusion
By focusing on part cost you can reduce the overall cost of your project. Remember, the goal is to balance functionality with manufacturability. Always consider the entire production process when designing parts, and don't hesitate to consult with manufacturing experts to find the best cost-saving solutions for your specific needs.
Implementing these strategies can lead to substantial savings in material costs, production time, and overall manufacturing expenses, giving your business a competitive edge in the market.
Enhance your parts using Captive Nuts!
Master the art of assembling laser-cut sheet metal parts with captive nuts - a cost-effective, tool-free method ideal for hobbyists and prototypers.
What is K-Factor?
Demystify K-factor in sheet metal bending. Learn its importance and how Fabworks ensures precise bends without complex calculations.
Fast Track Your Project .
Seamless process, unparalleled precision, unbeatable speed. Turn your design into reality by beginning your journey with us today.
or drag and drop
.STEP / .STP up to 25MB
Your file are safe, secure and retain all intellectual rights.