The Benefits of Countersinking in Metal Fabrication
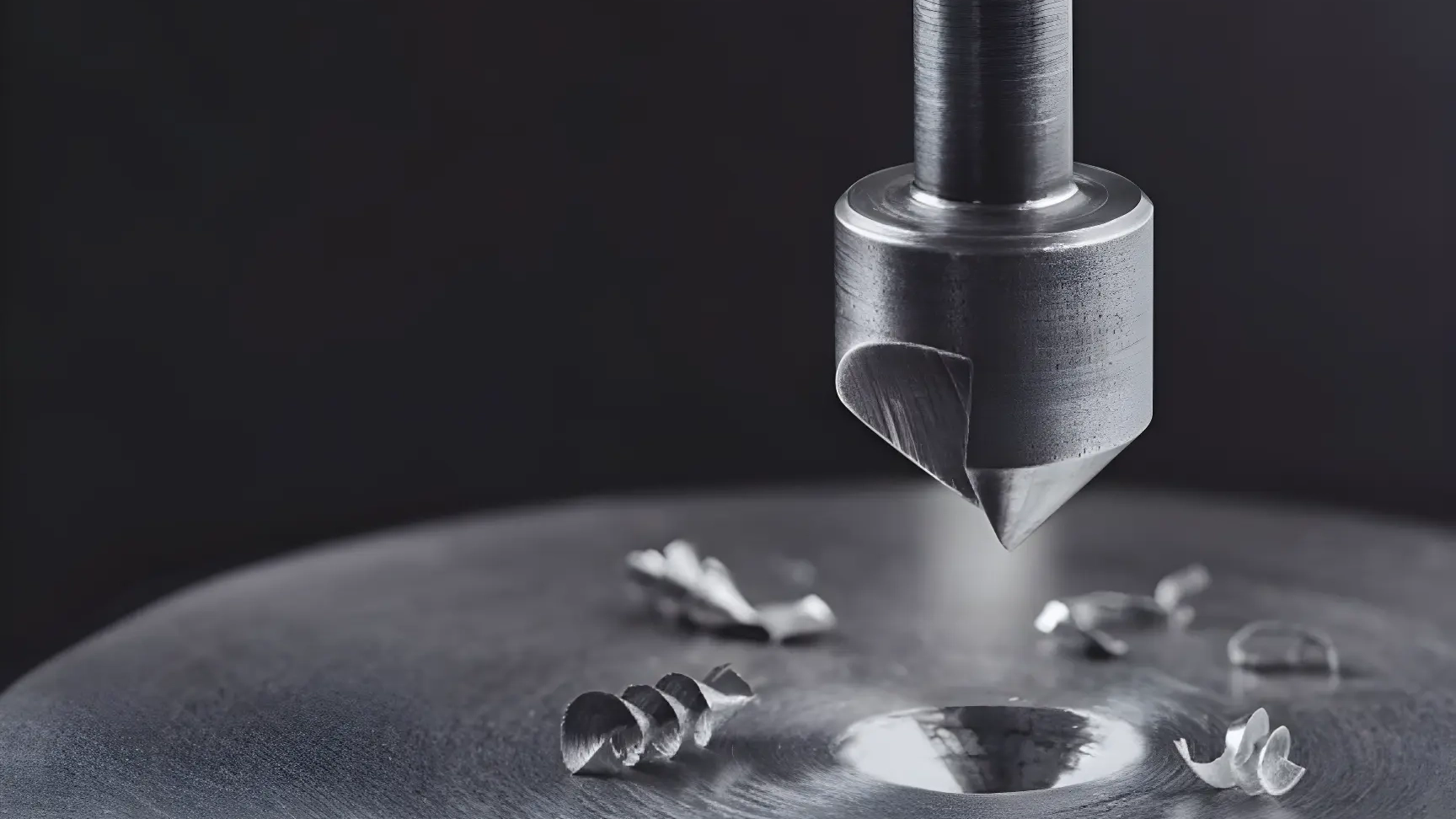
Countersinking is a game-changer in metal fabrication. It’s all about creating a conical hole that lets fasteners like screws and bolts sit flush with the surface. How’s this done? By enlarging the top part of a pre-drilled hole using a countersinking bit.
Why bother with countersinking? Simple. You get a smooth finish and increased accuracy. No more annoying protruding fastener heads. This is key for various applications.
- Electronics Enclosures: Keeps the surface clean and snag-free.
- Casings: Ensures a sleek, finished look.
- Machine Components: Provides accurate, secure assemblies.
Countersinking isn’t just about aesthetics, though. It’s crucial for ensuring your parts fit together perfectly and function as intended. Whether you’re working on prototypes or production, understanding countersinking can make a huge difference in the quality and performance of your projects.
Key Benefits of Countersinking
- Enhanced Appearance: Creates a clean, professional look, by embedding the fastener into the surface of the plate.
- Increased Durability: Shields fasteners from damage. With fasteners tucked into the material surface it prevents damage to the fastener heads.
- Structural Integrity: Maintains tight component assembly. Having a sloped surface also provides a greater surface area making contact with the bolt head lowering the chances of self-loosening.
- High Precision: Guarantees exact fitment and quality. Because of the conic shape, countersunk fasteners are self aligning, which means they naturally try and put themselves to the middle of the hole. This can either be a benefit or a drawback. If your design requires higher hole tolerance countersunk fasteners could be counterproductive, but if your design needs high accuracy when assembled countersinking allows you to align components without having to hold tight hole size tolerances.
- Reliable Results: Consistent accuracy across all projects. Because of the self centering effect of countersunk fasteners you can ensure consistent assembly between parts without spending time on extra alignment care.
Drawbacks of Countersinking
- Requires thicker material: Due to the nature of countersunk fasteners you can only use them with thicker materials depending on the bolt size. If you are trying to use a fastener larger than the material thickness can support you end up expanding the original hole size, causing assembly issues.
- Increased manufacturing time: Manually countersinking dozens of holes on dozens of parts can increase production time a decent amount. If production times are a concern we offer rapid turnaround, helping you meet tight deadlines without compromising quality. By integrating countersinking with our other services like tapping and laser cutting, we streamline fabrication for maximum efficiency. Learn more about our specialized sheet metal countersinking services to see how we can meet your project needs.
Choosing the Right Countersink Angle
The angle of your countersink can significantly impact the performance and appearance of your finished product. Here's a quick guide to help you choose:
82° Angle: The most common choice for general-purpose applications with imperial fasteners. It works well with standard countersunk bolts and provides a good balance between holding power and aesthetics.
90° Angle: Very similar to 82°, but usually found in metric fasteners instead of imperial.
100° Angle: Provides a shallower countersink, which can be beneficial in thinner materials or where you want to minimize material removal.
120° Angle: Used for specific applications like aircraft manufacturing, usually with countersunk rivets.
Important:
Summary
Countersinking is a vital technique in metal fabrication, creating conical holes to allow fasteners like screws and bolts to sit flush with the surface. This process not only enhances the appearance of products by providing a smooth finish but also improves structural stability, durability, and precision. It's commonly used in applications like electronics enclosures, furniture, and machine components where a clean, professional look and reliable fitment are essential. However, countersinking requires thicker materials and can increase production time. Despite these challenges, its benefits in improving product quality and performance make it a valuable technique in many projects.
Essential Checks Before Ordering Sheet Metal Parts
Optimize sheet metal designs with our pre-order checklist. Catch common errors and ensure manufacturability before submitting to Fabworks' laser cutting service.
Fast Track Your Project.
Seamless process, unparalleled precision, unbeatable speed. Turn your design into reality by beginning your journey with us today.
or drag and drop
.STEP / .STP up to 25MB
Your file are safe, secure and retain all intellectual rights.