How to attach Sheet Metal parts together.
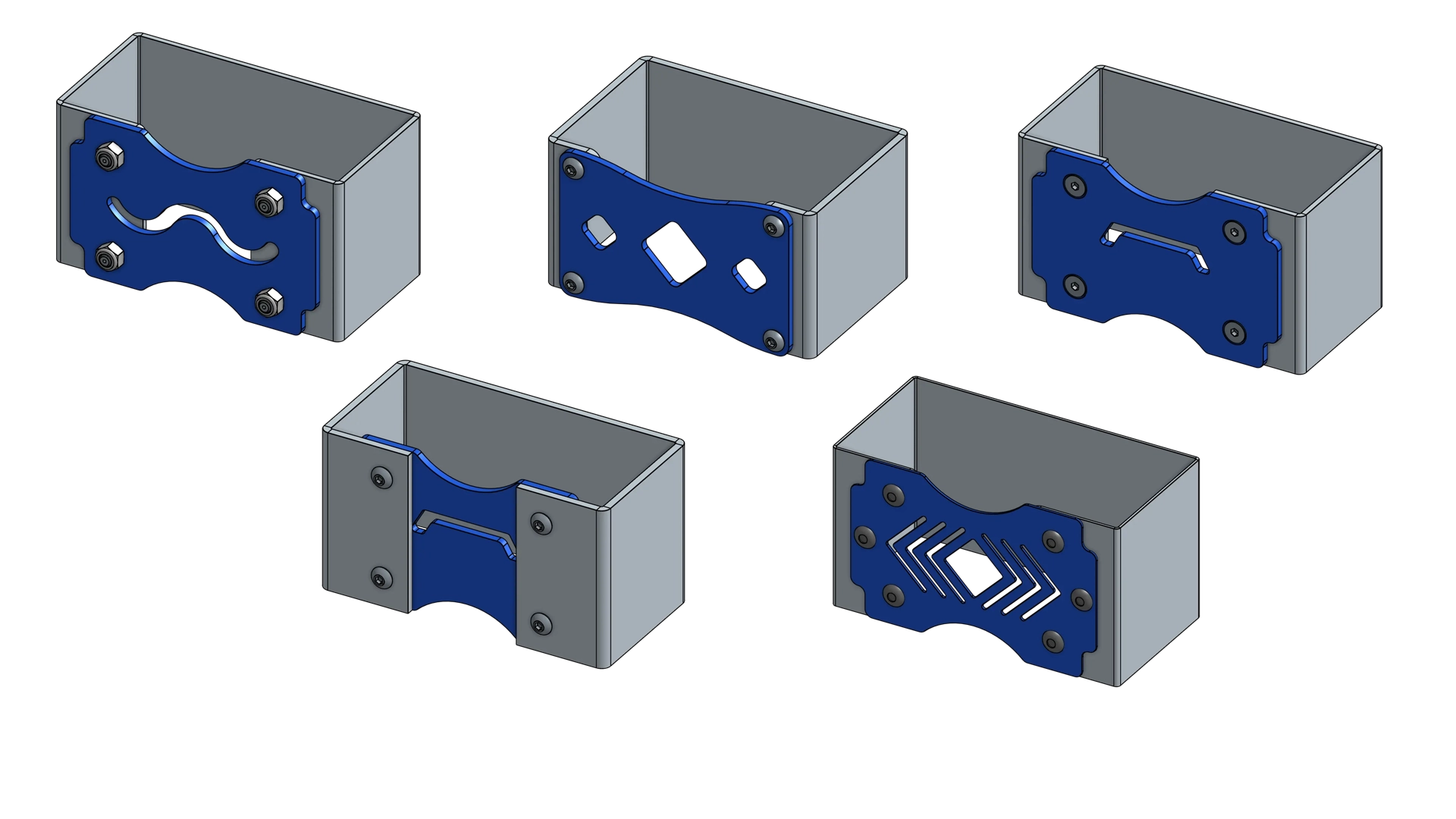
When it comes to assembling sheet metal components, designers and manufacturers have several options to choose from. Each attachment method has its own strengths and ideal use cases. In this post, we'll compare some of the most common techniques for joining sheet metal parts:
Tapped Holes
Tapping involves cutting threads directly into the sheet metal to allow for screw attachment. This method works well for thicker gauges and provides a clean, flush connection. However, it can weaken thin materials and may not hold up to repeated assembly/disassembly. Tapped holes offer a clean, integrated appearance and work with standard screws, allowing for easy disassembly. However, they require sufficient material thickness and can weaken thin sheets. The strength of the threads depends on the material properties.
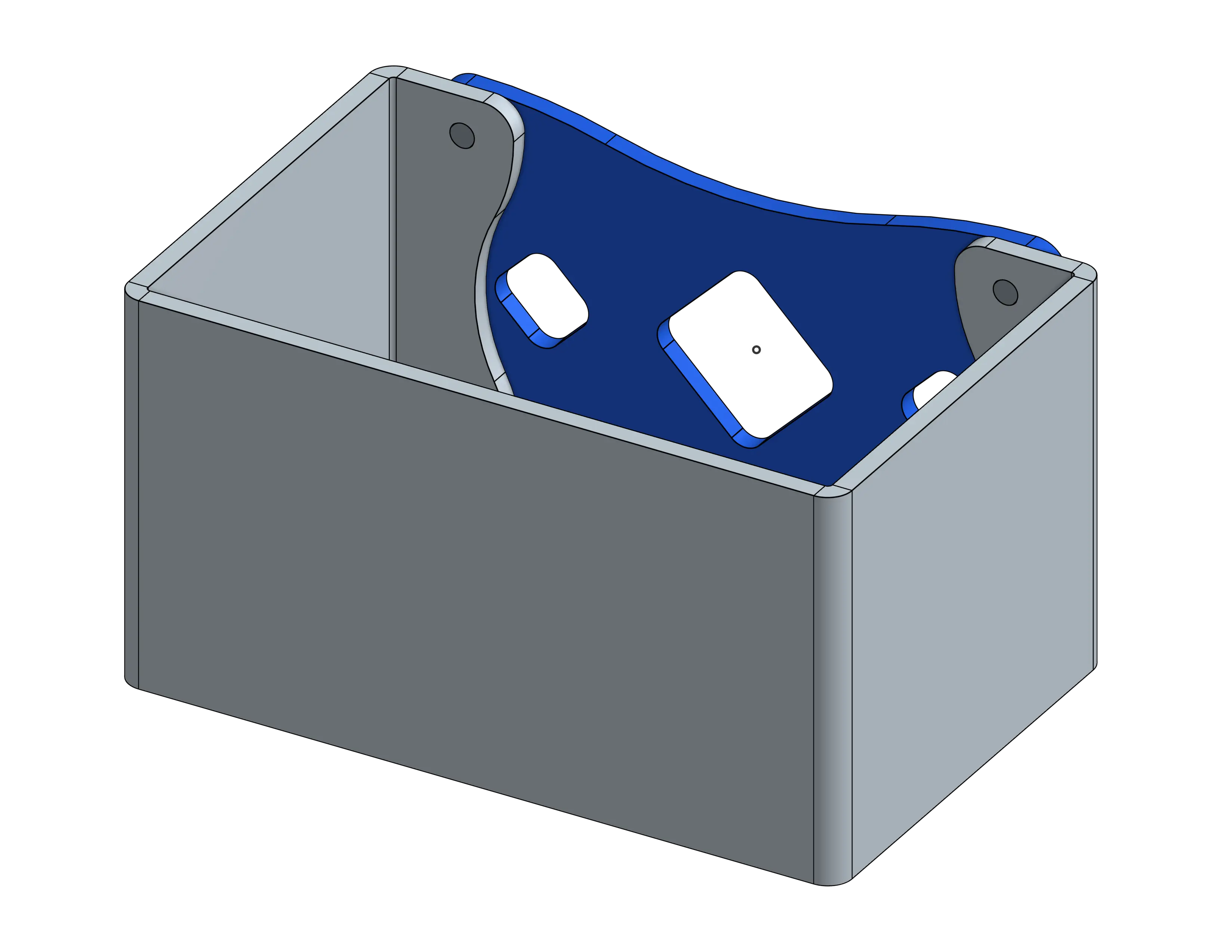
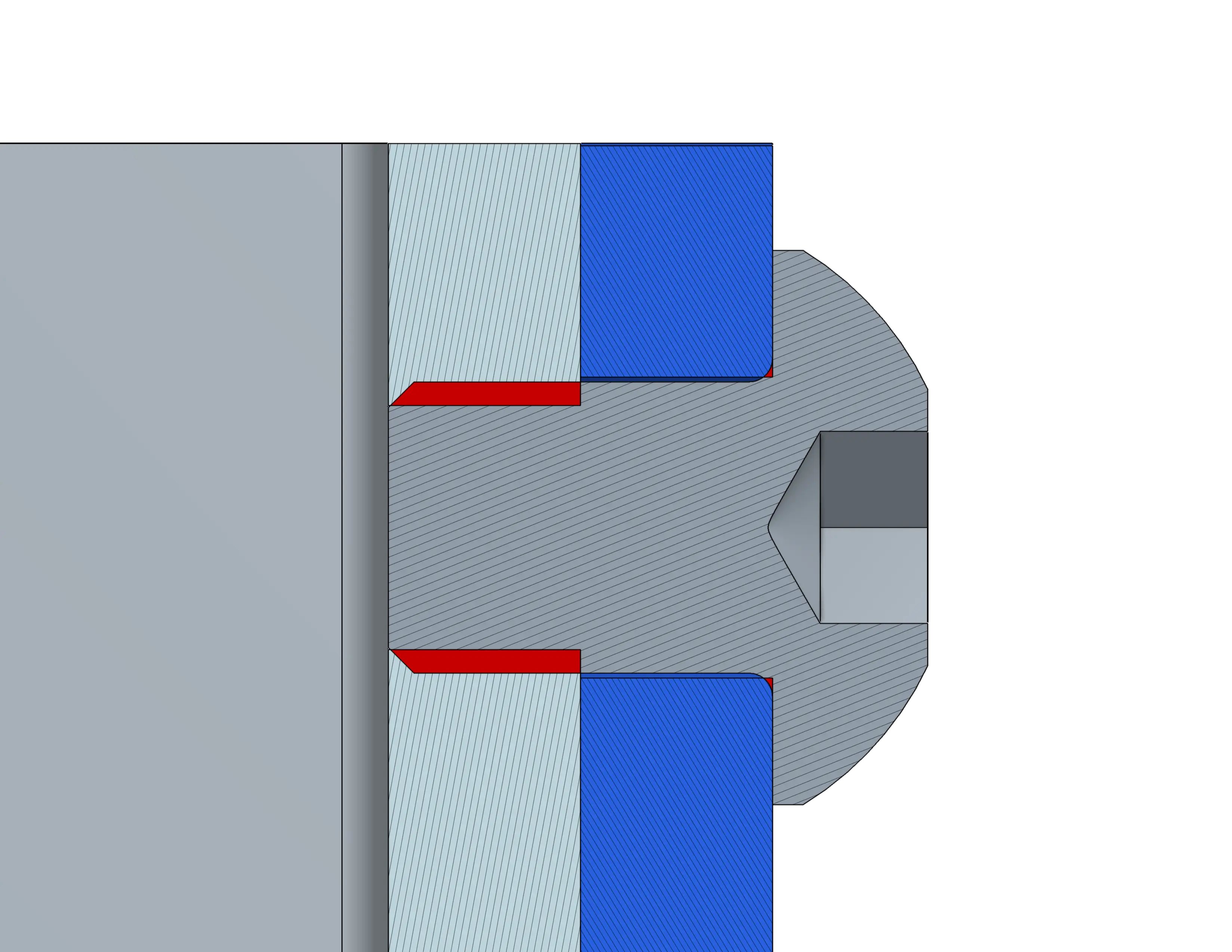
PEM Nuts
PEM nuts are press-fit threaded inserts that provide strong, reusable threads in thin sheet metal. They distribute load and prevent stripping better than tapped holes. These inserts offer stronger threads than direct tapping and work well in thin materials, allowing for repeated assembly and disassembly. However, they require special installation tooling and add some cost and thickness to the part.
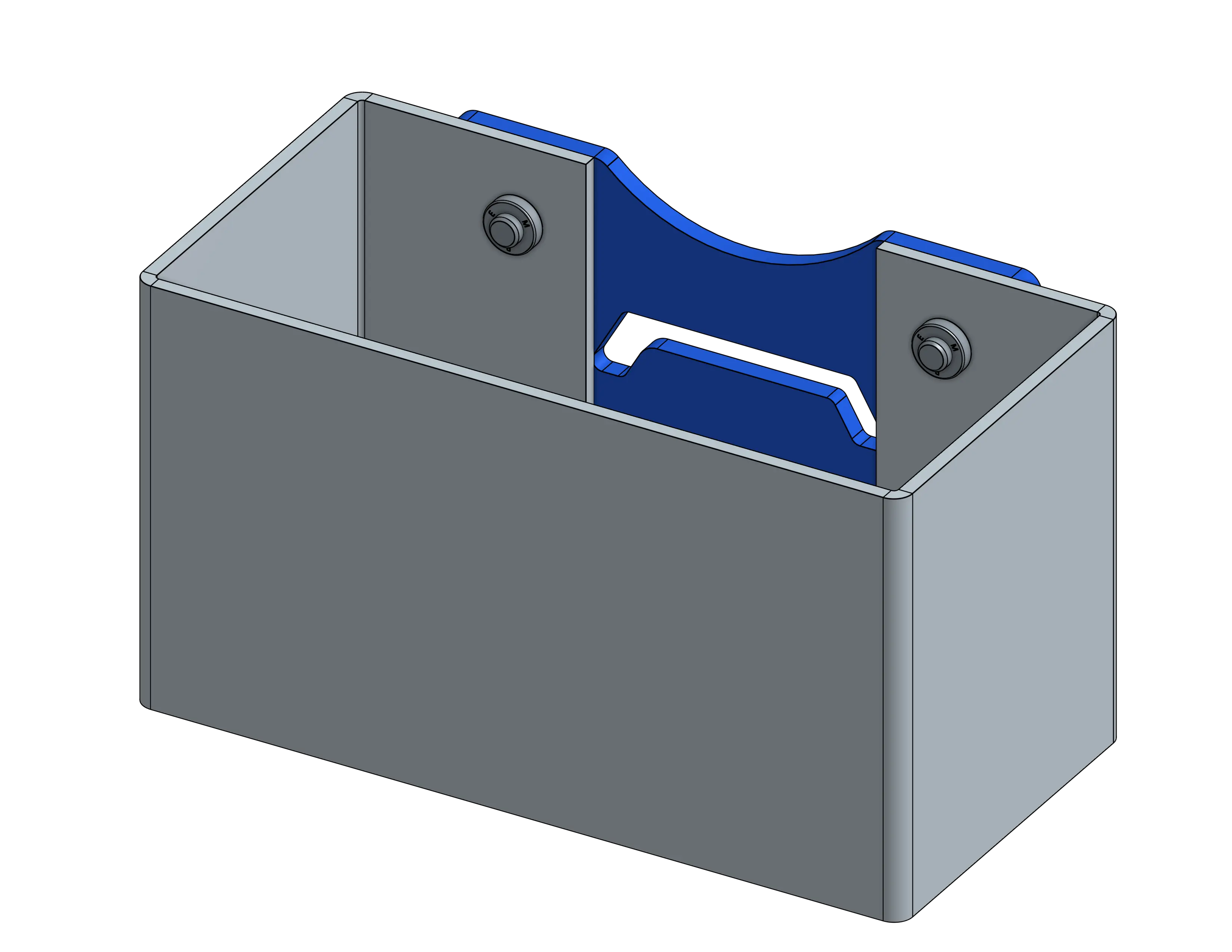
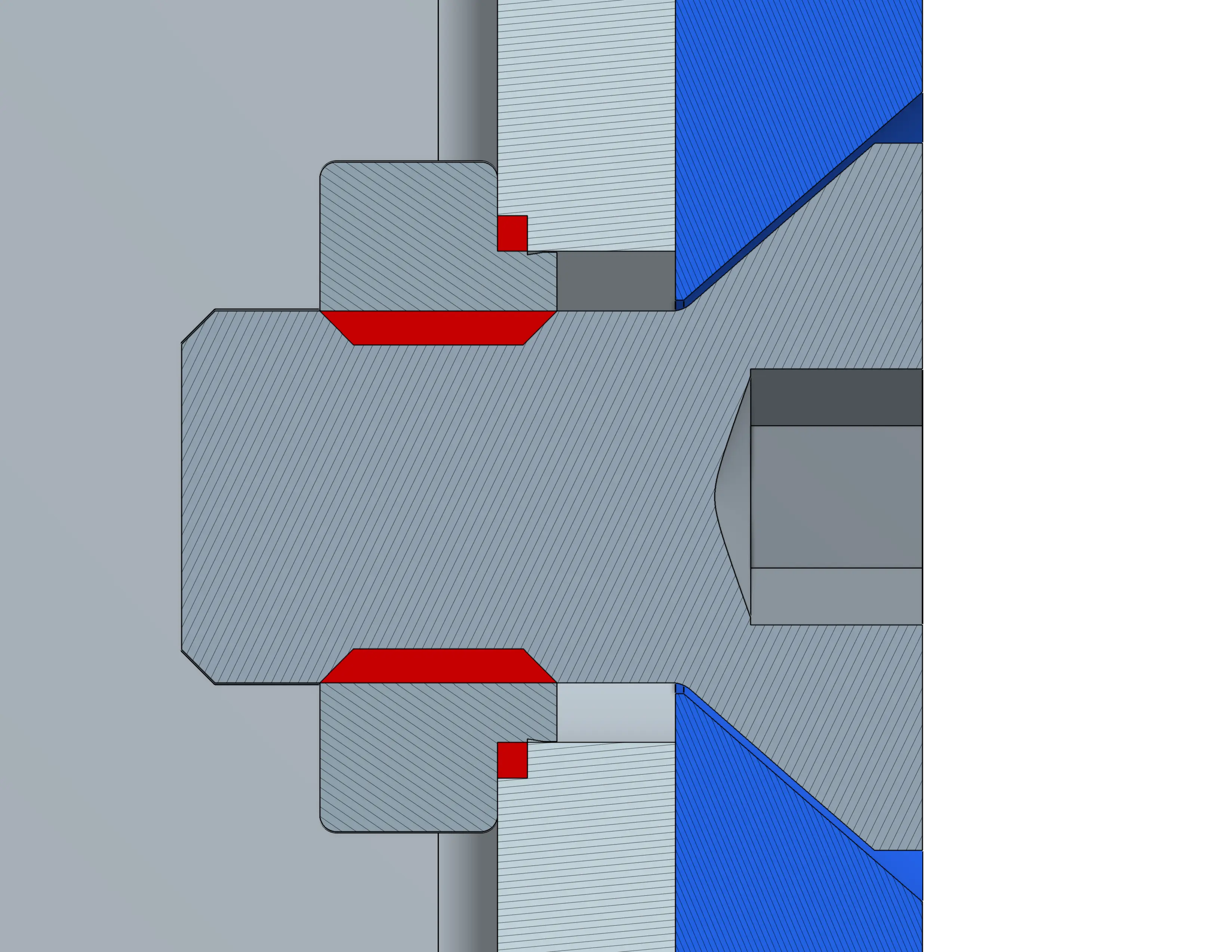
Standoffs
Standoffs can be used to attach two parts in multiple ways. The simplest method is acting like a regular standoff with threads to stack two parts on top of each other. The other way to use standoffs similar to PEM Nuts. By using a standoff equal to your material thickness you can get threads as long as the combined material thickness of the two parts, all flush with both surfaces, leading to a stronger threaded connection with the part.
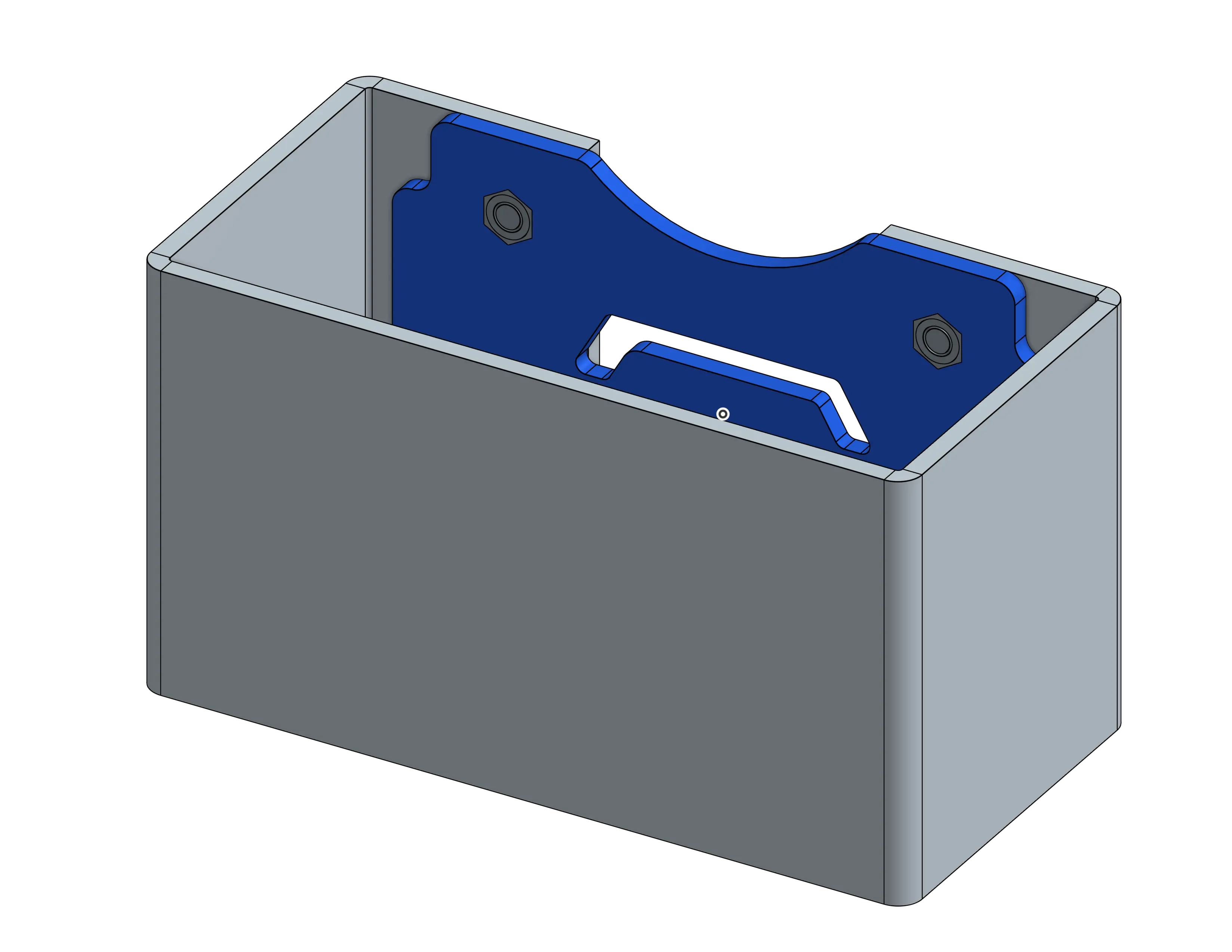
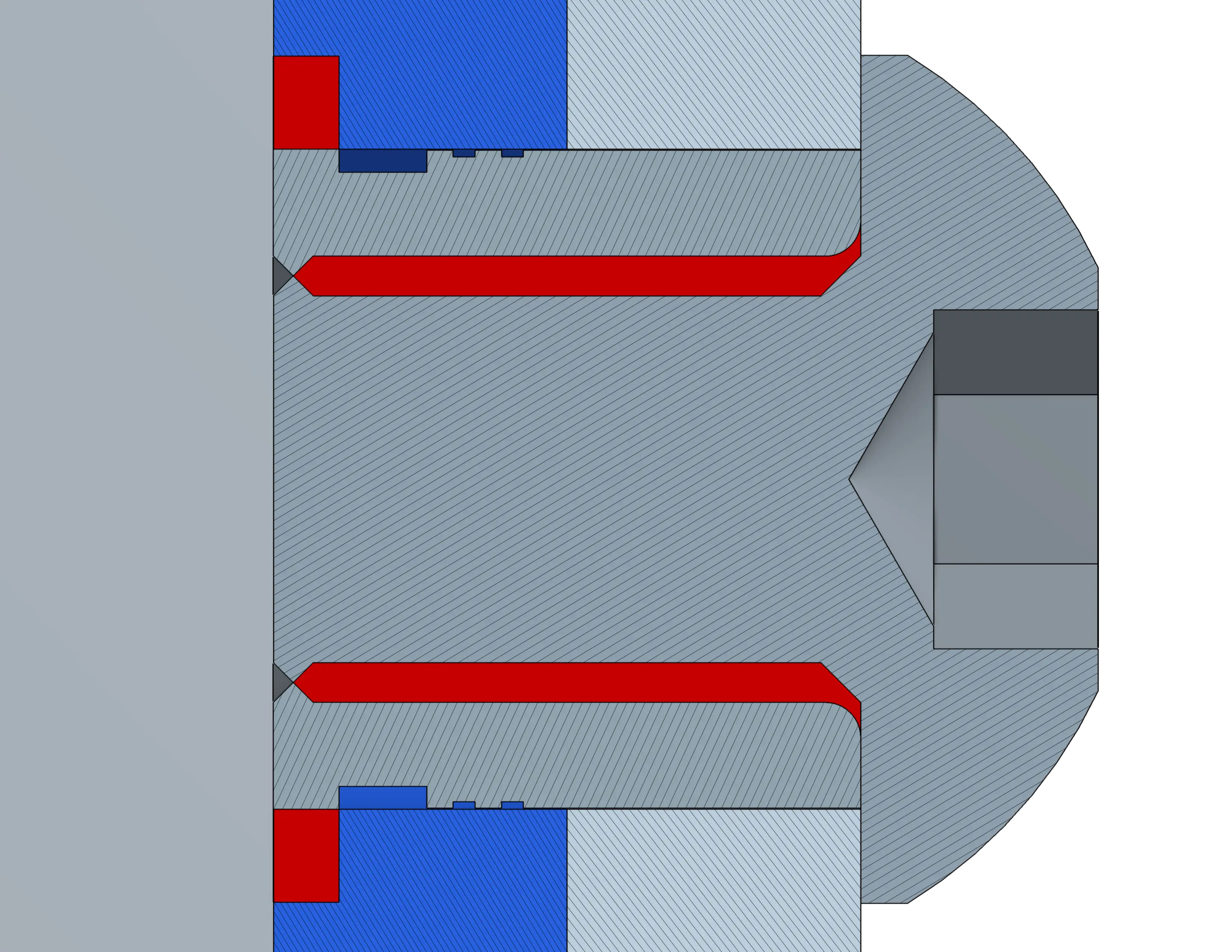
PEM Studs
Press-fit threaded studs provide male threads protruding from the sheet metal surface. They're useful for blind attachment or when female threads are needed on the exterior. PEM studs enable blind assembly from one side and create strong permanent threads, working well with thin materials. However, they are a permanent installation and protrude from the surface.

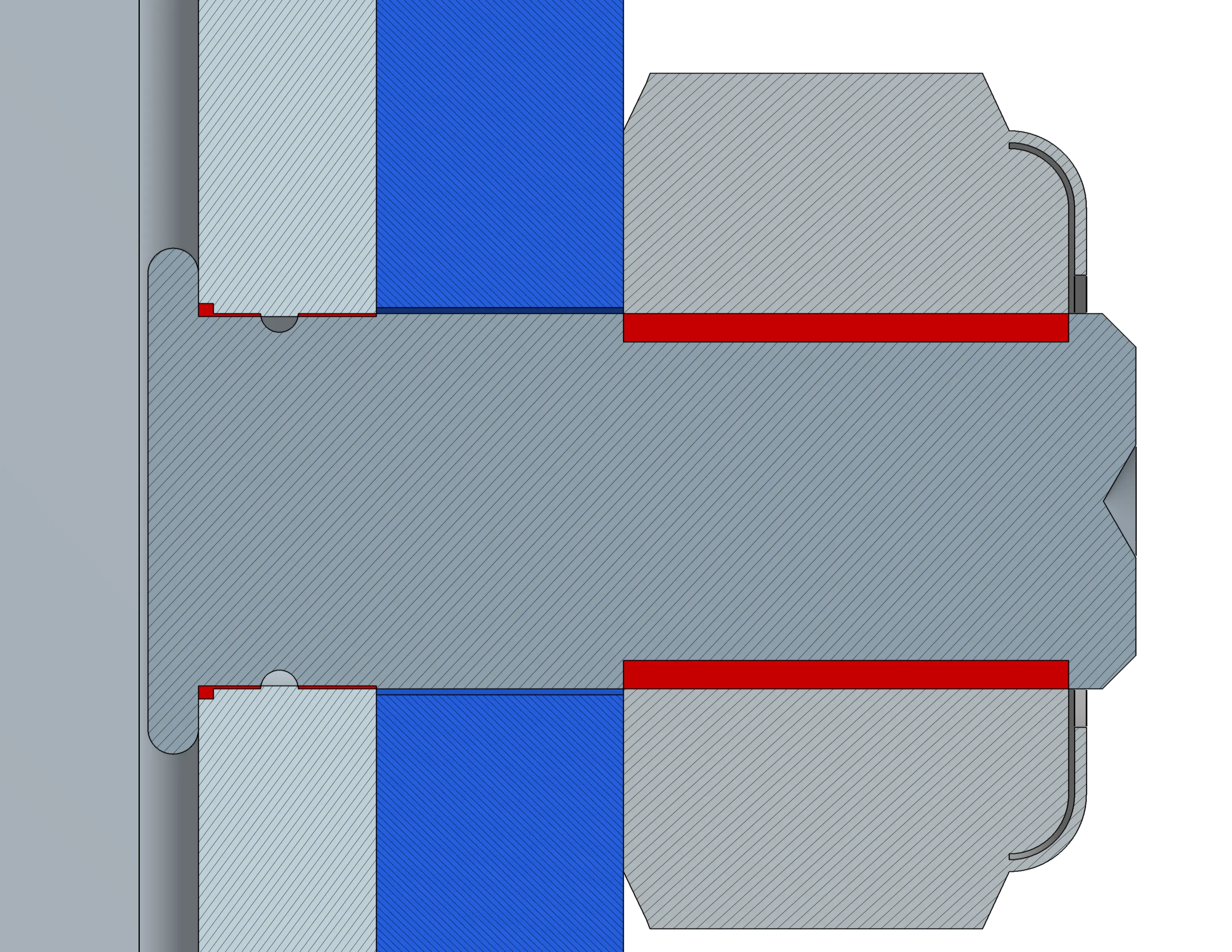
Rivets
Rivets provide permanent, strong connections between sheet metal parts. They work well for high-volume production but don't allow for easy disassembly. Rivets create very strong permanent connections and allow for fast installation in production settings. They also work well with dissimilar materials. However, rivets are not easily removable, require access to both sides, and can distort thin materials.
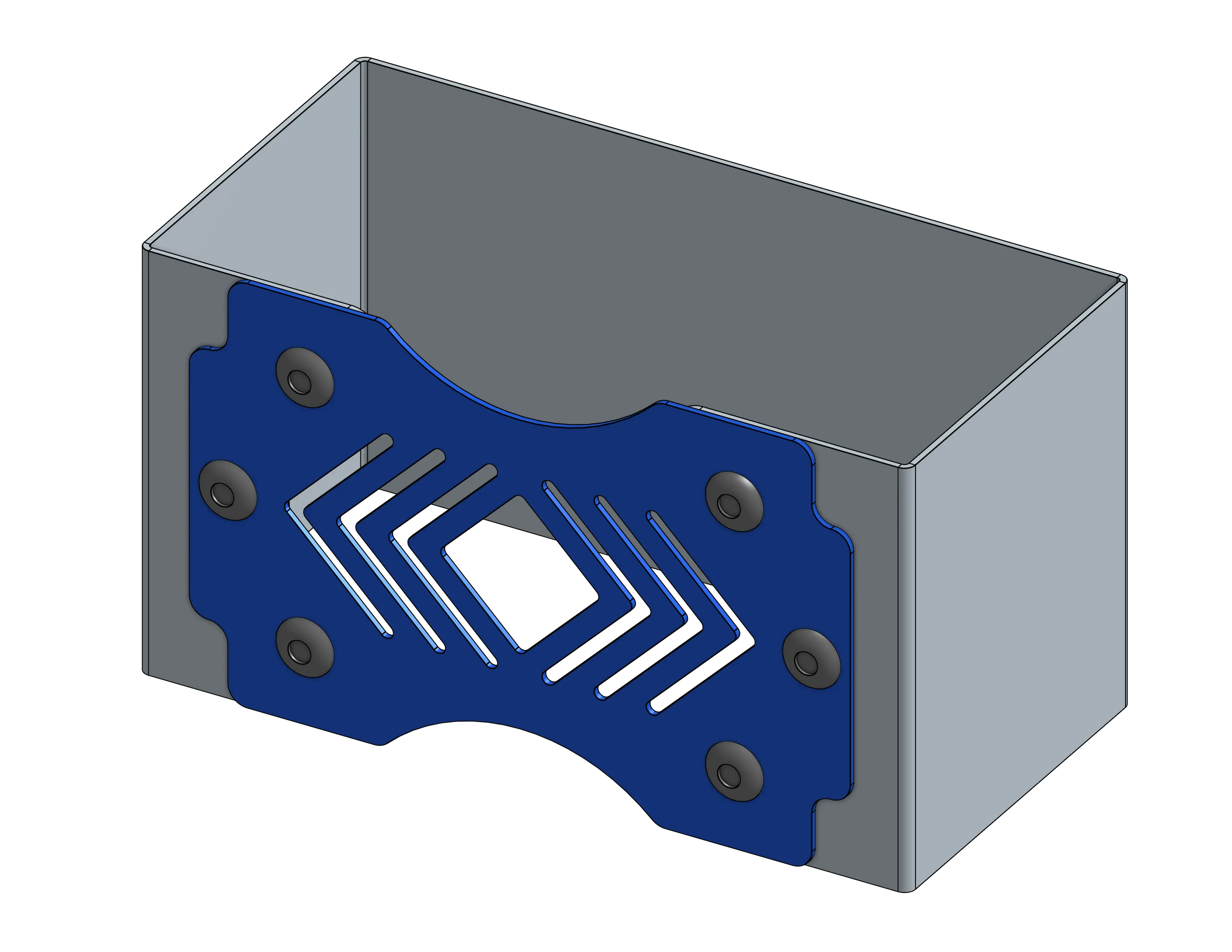
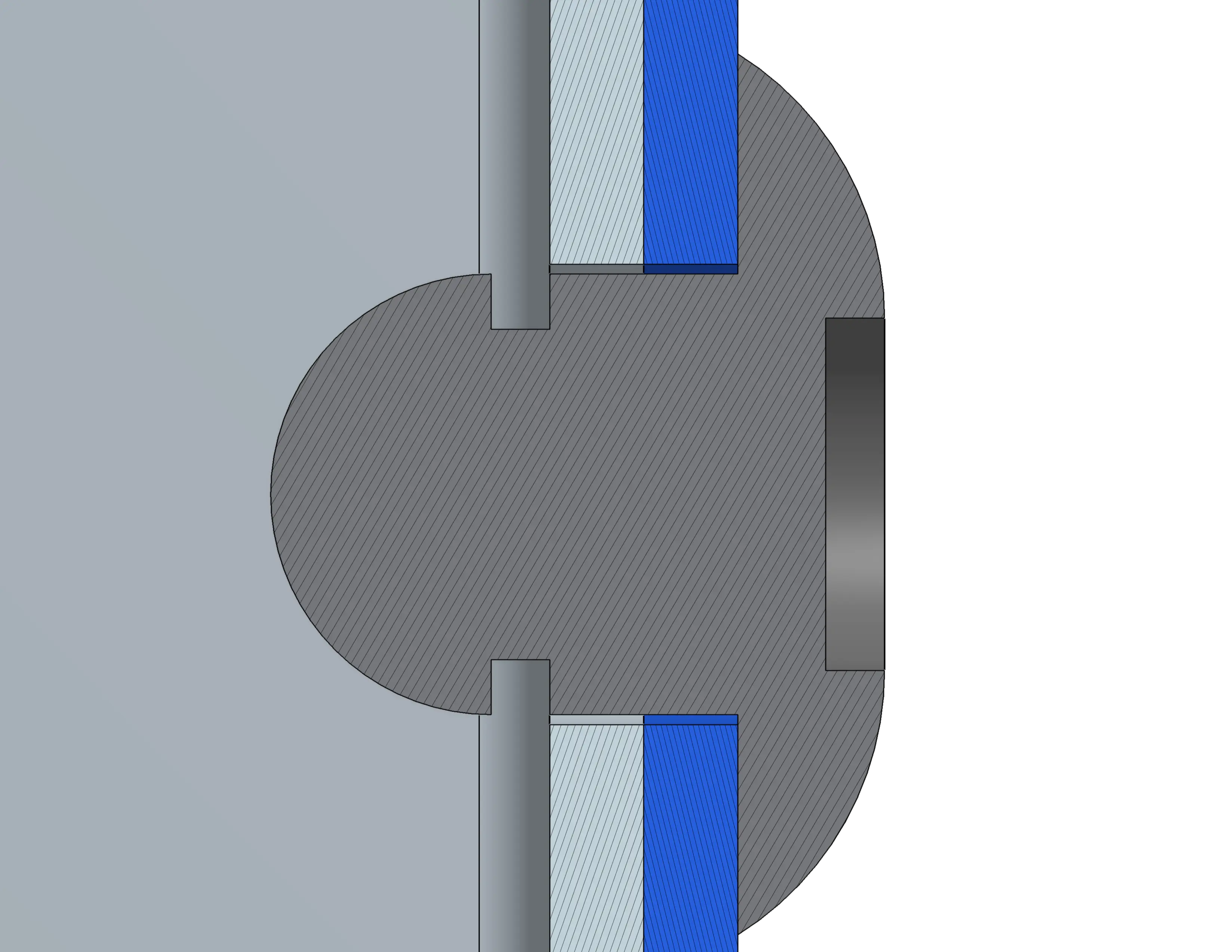
Welding
Welding creates strong permanent bonds between sheet metal parts. It's ideal for structural applications but requires skilled labor and can distort thin materials. Welding produces strong connections and can create sealed, water-tight joints with a clean, integrated appearance. However, it's a permanent connection that requires specialized equipment and expertise. Welding will also warp materials if not done carefully.
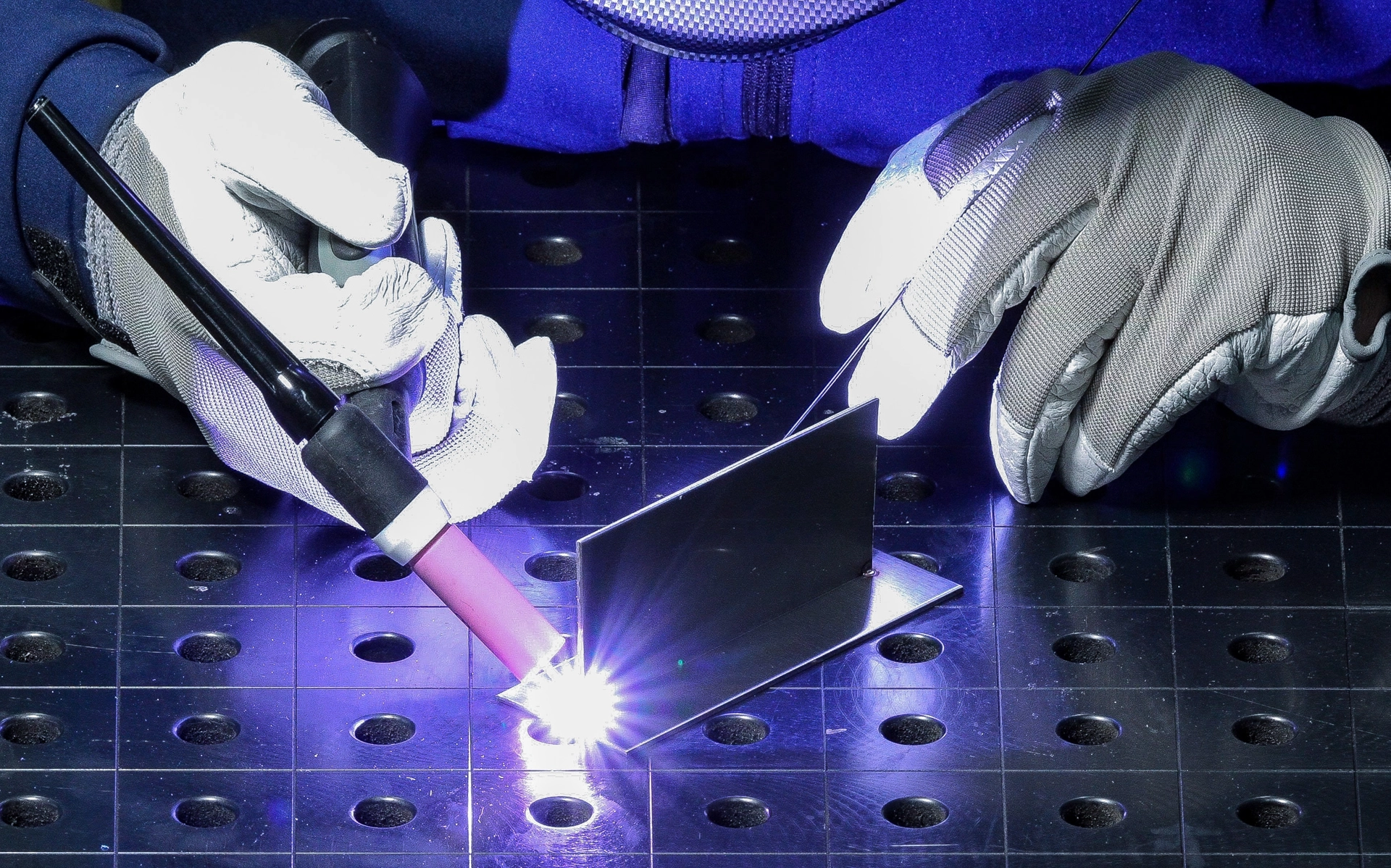
Choosing the Right Method
The best attachment technique depends on your specific application requirements. Consider factors like material thickness, load-bearing needs, assembly/disassembly frequency, production volume, cosmetic requirements, and environmental conditions. For precision sheet metal fabrication using many of these joining methods, Fabworks offers expert manufacturing services. Our team can advise on the optimal attachment approach for your project and provide high-quality laser cutting, bending, and hardware insertion to bring your designs to life. Let us know if you have any questions about selecting the right joining method for your next sheet metal project!
How to Prevent Rust on Laser Cut Parts
Discover effective strategies to prevent rust on laser cut metal parts, from material selection and protective coatings to design tips and post-production care.
Fast Track Your Project .
Seamless process, unparalleled precision, unbeatable speed. Turn your design into reality by beginning your journey with us today.
or drag and drop
.STEP / .STP up to 25MB
Your file are safe, secure and retain all intellectual rights.